Cabluri de date perfecte - "reteta" in opt pasi
In octombrie 2016 Lapp Group a achizitionat producatorul CEAM Cavi Speciali, lider in domeniul cablurilor de date destinate Ethernetului industrial si a cablurilor pentru magistrale de date. In cele ce urmeazveti afla mai multe despre procesul de fabricatie al acestor cabluri.
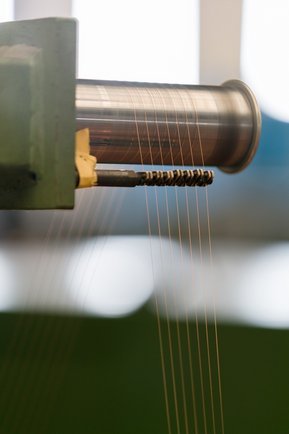
Conductorii cablurilor industriale de date sunt constituiti din lite fine din cupru, rasucite impreuna pentru a forma un toron.
CEAM Cavi Speciali este noua unitate a grupului Lapp specializata pe cabluri de date. Achizitionarea liderului in tehnologie din zona Venetia creste pozitia de lider a Lapp Group pe piata segmentelor cablurilor de date destinate conceptului Industry 4.0. La CEAM, aflata in Monselice, langa Padova, 110 specialisti dezvolta si produc cabluri din brandurile UNITRONIC® si ETHERLINE® pentru Ethernet industrial si magistrale de date, la cele mai inalte standarde. Afacerile profitabile sunt cheia de crestere a Grupului Lapp. Cablurile realizate la Monselice sunt foarte sigure, in termenii vitezelor de transmitere si a duratei de serviciu, datorita procesului de productie sofisticat, complet automatizat si a expertizei pe care CEAM o detine in aceasta zona de productie.
Noua companie Lapp isi deschide acum portile pentru ane arata cei opt pasi care duc la fabricarea cablurilor industriale destinate datelor :
Pasul 1 – Conductorii
Conductorii individuali incorporati in cablurile de date sunt confectionati din lite subtiri rasucite impreuna pentru a forma un toron. Sunt mai multe moduri de realizare a toronului iar numarul de lite folosit si grosimea acestora depinde de latimea de banda, flexibilitatea si diametrul exterior solicitat pentru un anumit cablu. Pentru cabluri performante si subtiri destinate Ethernetului, CEAM utilizeaza o structura cu 7 lite dispuse intr-o structura concentrica. Cu alte cuvinte, o lita dispusa central si alte sase lite dispuse tangent cu prima si intre ele astfel incat ansamblul creat sa se inscrie perfect intr-un cerc. In mod uzual, toronul de lite destinat conductorului este achizitionat de la un producator tert dar , pentru a obtine forma perfecta, CEAM isi produce singur toronul deoarece nici un producator nu poate executa precizia solicitata. Chiar si cea mai mica abatere de la forma perfect circulara poate conduce la deprecierea datelor, in special pe distante mari.
Pasul 2 – Izolarea
Masa plastica – uzual poliolefina – este extrudata in jurul toronului de lite, creand izolatia de conductor. Pentru cablurile de inalta calitate executate de CEAM se aplica o alta tehnologie prin extrudarea simultana a trei straturi. Primul si al treilea strat creeaza suprafete compacte, perfect etanse, ca niste straturi de piele, iar intre ele, stratul al doilea este spumat prin injectie cu azot uscat. Azotul uscat este un foarte bun izolator si are constante dielectrice foarte bune, mai bune chiar decat poliolefina. Se creeaza astfel doua caracteristici extraordinare: capacitatea scazuta care permite transmiterea datelor pe distante mai mari iar performantele izolatiei in referitor la rezistenta de izolatie permite reducerea grosimii acesteia, conducand in final la obtinerea unui diametru exterior minimizat. Pentru obtinerea unei caracteristici omogene in lungul cablului este vital ca bulele de azot sa aibe aceeasi forma si aceeasi densitate, respectiv dispunere in toata masa de izolatie. Pentru aceasta, CEAM a trebuit sa isi consolideze expertiza de-a lungul anilor. Exista si metode mai ieftine de obtinere a structurii “piele “– spuma –“ piele”, utilizand o metoda chimica, nu una fizica. Aceasta procedura implica utilizarea unui strat median care, in cursul incalzirii din timpul extrudarii creeaza bule de gaz prin descompunere termica. Aceasta procedura nu poate atinge precizia dimensionala si nici distributia uniforma creata prin injectia azotului, in consecinta, cablurile realizate prin tehnologia chimica nu pot atinge parametrii electrici de top. Mai mult, specialistii CEAM au descoperit ca durata de viata a cablurilor obtinute prin metoda chimica au o durata de viata inferioara celor realizate prin metode fizice.
Pasul 3 – Torsadarea
In acest pas, conductorii izolati individual sunt torsadati impreuna pentru obtinerea unei stabilitati si flexibilitati imbunatatite. Este foarte important ca lungimea unui pas de torsadare ( distanta dupa care un conductor din pereche a realizat o intoacere de 360 grade ) sa fie perfect constanta indiferent de pozitie, in lungul cablului. Este de asemenea esential ca sa nu existe miscare de torsiune a conductorului in jurul propriei axe deoarece aceasta conduce la fragilizarea izolatiei in timp. In mod obisnuit, conductorii sunt torsadati in perechi care la randul lor sunt impletite cu una sau toate celelalte trei perechi ( vezi pasul 4 ). Pentru cablurile de date speciale cu rate de transfer de pana la 100 Mbit/s, structura de stea este potrivita iar diametrul exterior al cablului este de doar 2,4 ori mai mare decat diametrul conductorului individual, conducand la diametre cu 40% mai mici decat in cazul cablurilor conventionale realizate cu doua perechi separate. In cazul cablurilor cu structura in stea, conductorii opusi sunt torsadati impreuna. Din descriere procesul ar parea simplu dar formarea stelei necesita utilaje speciale care nu sunt la indemana oricarui producator.
Pasul 4 – Impletirea perechilor
Cand rata de transfer de 100 Mbit/s nu este suficienta – de exemplu cand sunt solicitate cabluri Cat.6A sau Cat.7 cu 10Gbit/s – nu mai sunt suficiente doua perechi de conductori si sunt necesare patru perechi de conductori. Cele patru perechi de conductori sunt torsadate impreuna deoarece o structura de stea cu opt conductori nu este posibila din perspectiva proiectarii si rezulta o structura de manunchi flexibil si compact.
Step 5 – Ecranarea tesuta
Acest pas determina cat de bine va fi protejat cablul impotriva interferentelor electromagnetice. Lite subtiri din cupru nestanat sau stanat sunt tesute in jurul manunchiului de conductori intr-o maniera care aminteste de razboaiele de tesut. Procesul este extrem de rapid si creeaza modele vizuale fine. Pentru aplicatiile in care interferentele electromagnetice sunt critice sau cablurile sunt destinate freventelor mari, sub stratul de ecran impletit se adauga un strat de folie aluminizata cu acoperire de 100 %. La CEAM procesul de ecranare este complet automatizat si este suficient un singur operator care deserveste 10 masini de impletit ecranul.
O cheie variabila este unghiul dintre axa cablului si litele care formeaza impletitura ecranului. Daca unghiul este mare, cantitatea de cupru utilizat pentru confectionarea ecranului este de asemenea mare. In acelati timp, in aplicatiile cu parametrii dinamici ridicati,unghiul mare creste flexibilitatea ecranului si cablul suporta miscari repetitive . Unghiul mare este asociat cu costuri de fabricatie mai mari dar in acelasi timp este asociat si cu comportament mai bun la miscare sau cu raze de indoire mai mici. Daca nu sunt impusi parametrii de miscare, unghiul de tesere poate fi micsorat pentru economisirea unei cantitati de cupru si scaderea costurilor de productie.
Pasul 6 – Izolatia exterioara
Diferitele tipuri de materiale utilizate pentru mantaua exterioara confera acesteia diferite proprietati, adaptate la agresiunile la care poate rezista cablul, de exemplu stres mecanic, atac chimic cu diferite substante chimice, factori climatici sau radiatii ultraviolete. In timpul procesului de realizare a mantalei exterioare, un extruder care lucreaza la temperatura inalta este alimentat cu materiale plastice granulate pe care le topeste si le depune peste ecranul cablului, constituind mantaua exterioara care seamana cu un furtun strans peste ecran. Pentru realizarea cotelor dimensionale, o piesa calibrata indeparteaza, la iesirea din extruder, orice exces de masa plastica si asigura ca suprafata mantalei este lisa. Tot sistemul este monitorizat de senzori care asigura corelarea corecta intre viteza de inaintare a cablului si cantitatea de masa plastica injectata de extruder si asigura centrarea perfecta a cablului in interiorul mantalei. La iesirea din extruder cablul, cu o temperatura a mantalei in jur de 200 grade Celsius, este imersat intr-o baie de apa de racire lunga de 10 metri. Dupa zona de racire, un sistem bazat pe aer ventilat asigura uscarea perfecta a mantalei inainte ca produsul final sa fie bobinat pe tamburi.
Mai multe materiale sunt disponibile pentru realizarea mantalei exterioare a cablurilor destinate mediului industrial iar alegerea tipului de material are ca efect durata de serviciu a cablului. Pentru performante dinamice ridicate sau atunci cand cablul este destinat unui stres mecanic ridicat, CEAM utilizeaza poliuretanul. O alta optiune pentru realizarea mantalei pentru cabluri care vor lucra in conditii dure este utilizarea materialului patentat de Lapp sub denumirea “Robust” : acesta este foarte rezistent la temperaturi extrem de mici sau de mari, la stre mecanic, la grasimi naturale sau la solutii detergente si dezinfectante. Mai mult, murdaria nu adera la suprafata mantalei, facand-o usor de curatat, ideala pentru industria alimentara, acolo unde procesele de curatare sunt efectuate cu regularitate.
Mantaua cablurilor industriale nu este niciodata fina sau stralucitoare, de fapt se simte la pipait un pic aspra. Explicatia este data de avantajele legate de durabilitate, in particular aceste suprafete nu permit lipirea intre ele a cablurilor pozate in contact sau aderenta intre ele atunci cand se freaca unul de celalalt.
Pasul 7 – Marcarea
Odata racit, cablul trece printr-un cap de imprimare, asemanator imprimantelor de birou dar de mare viteza si inalta calitate. Textul care trebuie imprimat este trimis automat de la un terminal de catre operator. In timp ce unii producatori realizeaza imprimarea dupa baia de racire, la CEAM acest proces este total separat. Mai intai cablul trece printr-un proces de inspectie pentru a se elimina orice neconformitate a mantalei. Acest proces implica reincalzirea mantalei si calibrarea finala a acesteia pentru a se asigura o toleranta dimensionala cat mai mica si o durabilitate cat mai mare.
Pasul 8 – Impachetarea
Dupa terminarea procesului de marcare, cablurile sunt bobinate pe tamburi care la final sunt infoliati si marcati cu toate datele de identificare necesare.
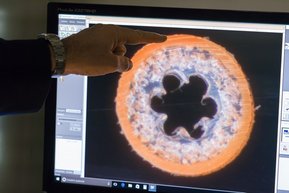
Procesul de izolare este foarte important pentru optinerea performantelor superioare. Prin injectarea azotului in stratul intermediar se optine o izolatie spumata cu performante electrice care asigura rate mari de transfer de date si dimensiuni reduse ale cablului.
Conductorii sunt torsadati impreuna. Structura de stea cu 4 colturi este ideala pentru realizarea in particular a cablurilor de date compacte.
In timpul realizarii ecranului, litele fine realizate din cupru sau din cupru stanat sunt impletite impreuna peste cablu pentru a realiza o protectie la interferente electromagnetice.